6 Overlooked Maintenance Tips for Heavy Equipment Owners
My dad owned a construction company when I was a kid, which meant summer break wasn’t really a break. One summer I was tasked with cleaning up an old asphalt paver. It took a couple days to get it as clean as possible. I greased it and told my dad it was all cleaned up. Of course, we did the classic walk around looking for dirty spots.
A few days later, I went to grab something out of the building where the paver was usually stored. It was gone. I was on the paving crew so I knew it wasn’t out on a job. I ran up to my dad and asked where it was. His response? “Oh, I sold that. Sold it for enough to buy a new and better one.”
Certainly, keeping your equipment clean is only one of the few overlooked aspects of heavy equipment maintenance. In my experience, adhering to these six maintenance practices increases your return on investment (ROI) and extends the equipment’s life.
1. Maintenance Log
Companies both big and small rarely keep in-depth service logs. Sometimes workers keep track of the basics, like repairs and oil changes. To maximize your ROI, it is critical to keep track of maintenance. It’s far too difficult to remember, and it gets harder the more equipment you have. MyAMSOILGarage is a handy (and free) tool for tracking maintenance and services. Another benefit of maintenance logs? You can show potential buyers the equipment’s track record when it’s time to sell.
2. Washing/Cleaning
Washing and cleaning your equipment has significant benefits. First, mud and dirt can make it difficult to watch for fluid leaks, broken parts and other safety issues. Extended exposure to mud, dirt and dust can also accelerate rust formation and wear. I also highly recommend applying AMSOIL Heavy Duty Metal Protector on important areas for an added dose of protection.
3. Grease
While most workers grease equipment periodically, they may not use a quality synthetic grease that resists impact and washout. If you’re hard on equipment, upgrade to AMSOIL Synthetic Polymeric Off-Road Grease or Synthetic Polymeric Truck, Chassis and Equipment Grease. They offer resistance to impact, helping prevent the grease from pounding out in heavily loaded, extreme applications. They’re also recommended for extended service intervals, which helps reduce downtime.
4. Tires and Tracks
Tires – after discovering how much tires for heavy equipment can cost, I haven’t felt bad for the guy replacing tires on his Toyota Camry since. Sets run in the thousands, and you likely won’t find a “Buy 3 Get 1 Free” deal. Take care of them by checking the tread and inflation (psi) daily.
Tracks – Keep them clean! Get a narrow shovel and, if you can recruit one, a child who can dig into all the narrow spaces to get the dirt out (that’s what my parents did). Try to avoid slopes, blacktop and concrete. Plus, try not to spin the tracks. I realize that’s not possible in the real world, but I still encourage being mindful of it.
5. Air Filters
From working at AMSOIL, the phrase “an engine is an air pump” is ingrained in my brain. That said, the air entering the engine requires filtration, especially considering the constant dirt and dust on a work site. (And, if you aren’t kicking up dirt and mud in your loader, you’re not really working!) Contaminants can breach the engine and slowly scour away metal components. It’s just a matter of time until something fails. Check your air filters often.
6. Cooling System
Like the cooling system on your car or truck, the cooling system on heavy equipment is often overlooked. Proper cooling-system maintenance is essential in both diesel and gasoline applications. In diesel applications, pitting, overheating, over-cooling and cracked heads are just some of the common cooling-system catastrophes. AMSOIL Heavy-Duty Antifreeze & Coolant offers an extensive service life of 600,000 miles/12,000 hours of operation/six years in heavy-duty and off-road applications.
7. Bonus Round: Fluid Analysis
Conducting fluid analysis provides a number of different benefits, including…
Maximum drain intervals
Long equipment life
Reduced instances of major mechanical problems
Increased resale value
Oil Analyzers Inc. has many options for testing. Check out the OAI user guide for more details. Fluid analysis is well worth the investment in comparison to the investment of heavy machinery. Fluid analysis can help identify potential sources of contaminants while providing an idea of what mechanical issues may be looming.
These are just a few of the life lessons I learned during my summer “breaks.” It all boils down to performing those often-overlooked maintenance tasks (like cleaning equipment) to maximize the value of your assets.
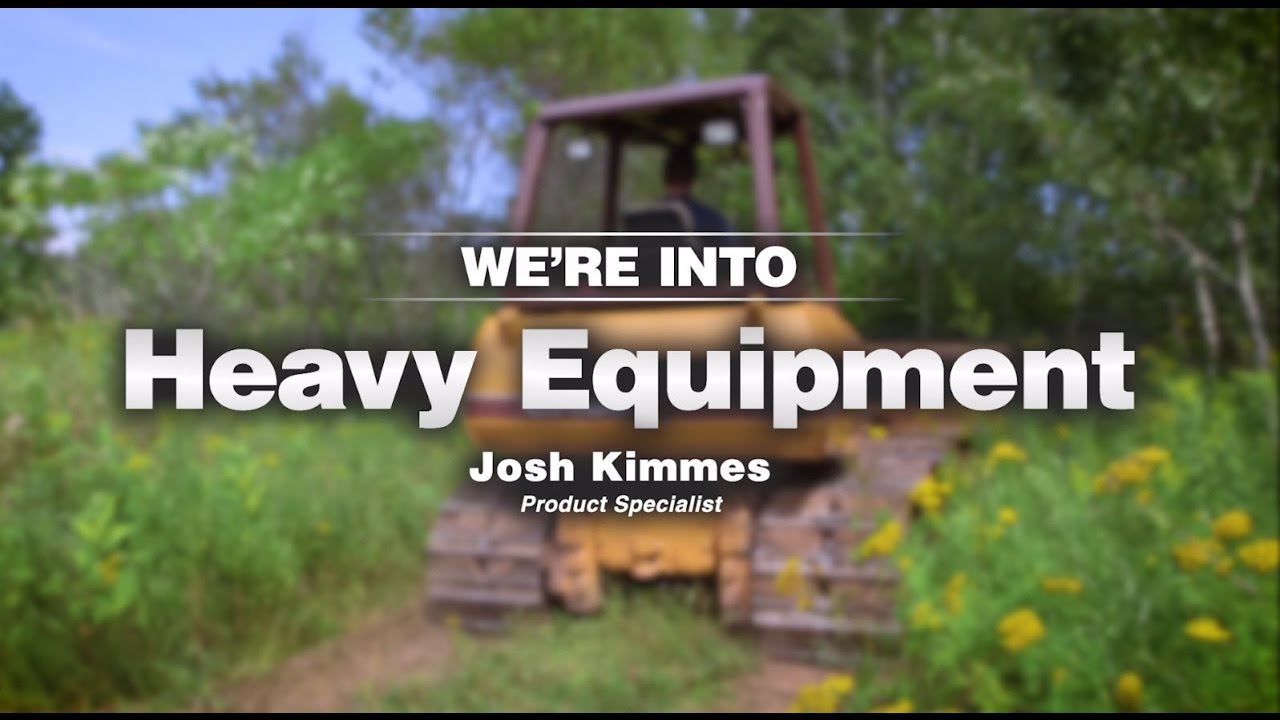